How to minimise the impact of batteries in micromobility
Shared mobility thinks of itself as green although Lithium-ion batteries still come under scrutiny. Here's how operators can optimize battery design, day-to-day operations and end-of-life management to wow cities and fight climate change even more.
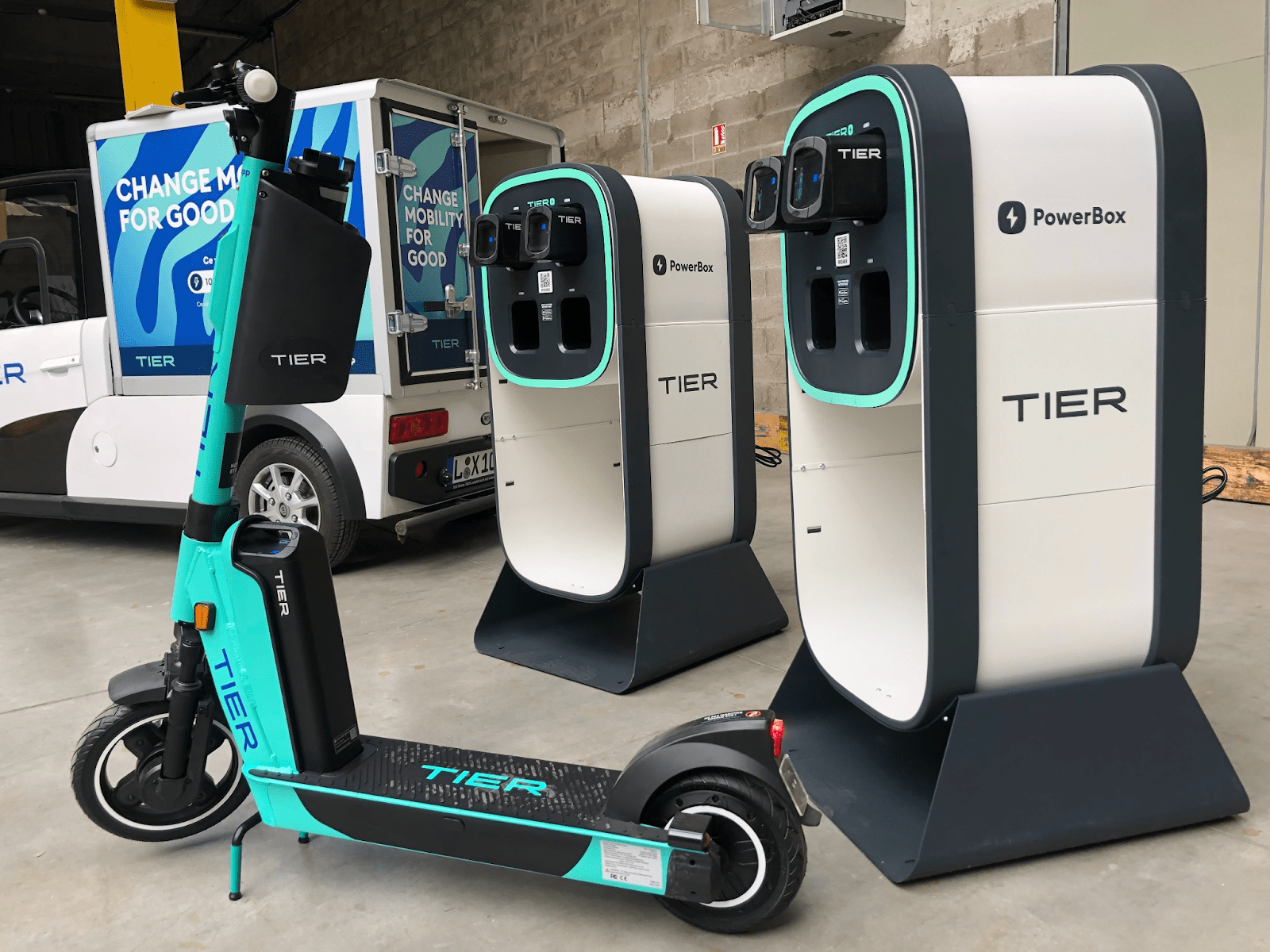
Since its inception, the shared mobility community - of which Fluctuo is a proud member - has branded itself the green transportation solution. The electrification of entire fleets has only strengthened this claim. As a movement, we have always been a few steps ahead: only recently did the European Parliament vote in favour of a complete ban of ICE by 2035.
But we haven’t figured it all out.
Electric vehicles are not the ultimate environment-friendly solution. Yes, they use a cleaner energy source (depending on how the energy is produced) and they do not produce harmful emissions…but they do use extra components, of which, one comes under particular scrutiny from sustainability analysts: Lithium-ion batteries.
From the lithium mines of Australia and Chile and the cobalt mines of the Democratic Republic of Congo to the cell factories in Asia, battery production is not CO²-free. In some cases, such as in the DRC, it can even be morally onerous. And although R&D to improve existing technologies and develop new solutions (e.g. solid-state batteries) is being carried out very quickly, there is already a lot that shared mobility players can do to lower the environmental impact of battery usage, from design, to day-to-day operations, and end-of-life management.
Designing the best battery
When designing a battery, the first step is to define its capacity. Of course, operational efficiency and cost cannot be completely ignored in the face of environmental impact. If we did that, shared mobility simply wouldn’t be viable.
The bigger the battery, the more range and the lower the charging frequency. This brings obvious benefits in terms of vehicle availability, and ‘consumes’ the average of 500 charging cycles of a Lithium-Ion battery slower, extending its lifespan. When it comes to the environmental impact of production and usage, two small batteries will have a similar carbon footprint to one large battery. : (that is to say, two 500Wh batteries will last as long as one 1kWh. But by reducing the operational tasks (battery swaps, charging, etc), you reduce both the carbon footprint of the maintenance trips carried out with heavy vehicles and mitigate the risk of misuse or mishandling which could reduce their lifespan.
Weight is another crucial factor. A maintenance van that is able to carry 50 500Wh batteries will only be able to serve 25 1kWh ones, while some vehicle types have to comply with weight limits including the battery, such as scooters in France (30kg maximum). The available volume is also limited by design on a scooter or a bike, setting the upper capacity limit between 650Wh and 1kWh according to most operators. George Kalligeros, TIER’s Director of Hardware Engineering, confirms that “most of the vehicles are using a 690Wh battery”, while “Pony bets on 600Wh ones, with 2 battery slots on the Double Pony”, according to CEO Paul-Adrien Cormerais. Both companies confirmed their desire to increase battery energy density to offer more capacity, which would bring them closer to Lime’s latest 1kWh model.
With the constraints on volume and size, new technologies must be developed to improve energy density. Over the last 12 years, Lithium-ion battery density has increased from 55 Wh per litre to 450 Wh per litre. Despite being one of the best solutions today, it will soon face competition from other solutions such as Lithium-Metal solid-state batteries, which would theoretically double the energy density of Lithium-Ion batteries.
Although it sounds like science fiction, moped manufacturer Gogoro is already trialling a Lithium-Ceramic solid-state model...
Optimising battery management
Most operators were quick to drop fixed batteries - and the constraint of moving the whole vehicle to charge them - for swappable ones. This widely adopted model is based on an operation warehouse in the outskirts of a dense operation area, where electric vans or cargo bikes bring batches of batteries back to the warehouse, or sub-hubs, to be charged.
The environmental impact of this strategy has been challenged, as you need more batteries than vehicles to operate a fleet. Around 20 to 30% more batteries are required to run an efficient service (depending on the vehicle ridership). More batteries mean a higher environmental impact, that was one of the main arguments for Bird to keep operating its home-designed scooters with fixed batteries, though the company started to introduce new models with swappable ones. But the comparison has to be made for a number of available vehicles, and Bird or Superpedestrian also need extra scooters to operate with a fleet availability close to the number of desired scooters on the street per day.
Back to the warehouse. Batteries arrive from the field, are placed on shelves and charged. Many operators are already partnering with green energy providers, such as Dott with Primeo Energy or Lime with Planet Oui in France, to match their sustainability goals by lowering the carbon footprint of the energy they consume.
During charging, the Battery Management System (BMS, the brain of the battery) calculates a few basic parameters from current, voltage and temperature readings:
- State of Charge (SoC, or real-time capacity)
- State of Health (SoH, an estimation of the real-time battery performance)
Many operators are still struggling to predict performance. For now, they can only see the state of the battery at a specific time, but what if they could see the health of each cell, and optimise charging cycles to understand how their fleet of batteries is ageing? Connected batteries and AI-based software can solve these challenges.
The first step is to get the data from the battery fleet. Gouach, a French start-up producing micromobility batteries, has developed a Bluetooth and WiFi-connected model, allowing data transmission, whether they are attached to a vehicle or not.
Other operators are developing smart chargers to get the data: based on its experience with the Power Box, launched in partnership with local shops in several European cities, TIER’s infrastructure R&D team has developed a similar smart battery charging station to be used in its warehouses.
“Understanding our battery fleet lifecycle better is crucial for our services to be more profitable and sustainable. We are investing in R&D to develop the capability to collect battery data during charging, which can be later analysed for insights.”
— George Kalligeros, Director of Hardware Engineering at TIER
Interestingly, TIER is also partnering with Swobbee, the leading manufacturer of smart battery charging cabinets. Their solution allows customers to get the data from the connected batteries, but CEO Thomas Duscha confirms that “the company has created a software and hardware platform for battery monitoring and data collection”, a solution required to cut on the cost and answer the warehouses' needs.
AI-based software offers massive potential for smart battery management. Already used in the energy or automotive industry, it might soon convince shared mobility operators:
“We are already collaborating with some companies in the industry to achieve two main goals: add a safety layer in battery charging, and improve the lifetime thus the sustainability of the batteries by up to 25%”.
— Kai-Philipp Kairies, CEO of Accure
Through structured analysis of operational battery data, software such as Accure’s Battery Analytics enables extensive assessments, such as early failure prediction, performance benchmarking or lifetime optimisation. Batteries become predictable even at a cell level, helping to define the point of no return for a battery, where it becomes unsustainable (financially and/or ecologically) to operate.
When is it time to call it a day on a battery?
Imagine that your battery lifecycle management software suggests that a battery should be taken out of rotation. But wait. In most battery failure cases, 80% of the battery components work perfectly. This is what drove Gouach’s CEO Alexandre Vallette to develop a fully repairable battery. After two years of R&D, the battery was ready, making battery repairs possible and affordable.
The French start-up, which entered the shared mobility industry with partnerships with pony and Dott, has developed the first micromobility battery with no soldering or cables. It makes every component easily swappable, up to a single battery cell. Gouach claims that its battery architecture saves 70% of its total carbon footprint! Thanks to a WiFi connexion, each component of a Gouach battery can be monitored through a management platform.
Given the current ‘environmental impact’ requirements in any shared mobility tender, operators are quickly realising the benefits of such a technology.
“[Gouach] is in talks with major shared micromobility operators to become their battery providers. With Batteries-as-a-Service (BaaS), we are taking over battery lifecycle monitoring and end-of-life management from operators, one of their main pain points.”
— Caroline Mirtain, CMO at Gouach
Swobbee CEO Thomas Duscha agrees, “with our BaaS model, we are managing a battery way more efficiently than a single customer would do, thanks to our solution and expertise”.
To date, Pony is the only operator to trial Gouach's solution in real life. Pony’s scooter fleet in Angers (FR) is equipped with repairable batteries.
“With a battery swap every 3 days, the theoretical lifespan of battery cells should be above 4 years. So we realised that early failures were coming from other components such as the BMS or the fuse. We were dying to find a repairable battery”.
— Paul-Adrien Cormerais, CEO of pony
If, after 6 months, it is still too soon to assess the impact, both companies will collaborate in the long-term to improve the battery and adapt battery management software to the operators’ usage.
Other companies might follow suit to develop repairable batteries. TIER is working on it, though George Kalligeros is still cautious about its future adoption: “If there is no question about the technology’s environmental benefits, but theft and vandalism are a concern. We have already faced such issues with regular batteries, and it might get worse if people have easier access to the battery cells”.
Other companies have developed enough knowledge to offer repairs for regular (ie. soldered) Lithium-Ion batteries. Doctibike, a French start-up created in 2016, refurbished 40,000 micromobility batteries in 2021 alone, including TIER and Voi’s. But the diversity and architecture of those batteries are a real barrier to industrialising the process.
End-of-life battery management
Batteries which are not usable on electric vehicles anymore might still be useful for other purposes. Whilst a scooter or electric bike requires enough range and power, ‘tired’ batteries can have a second life in battery storage installation, where their lifespan can be increased by a decade or more. The carbon footprint of its production and usage to power mobility services will then become negligible. All the companies we have been talking to are exploring this opportunity, though the current fleet of shared electric vehicles is far from being enough to power large battery storage power stations.
Nonetheless, smaller installations supporting wind or solar power plants, or acting as backup generators in remote areas with an unreliable grid, would still make sense. Acciona, the Spanish company already active in renewable energy and shared mobility with its moped services, was the first to announce a large-scale program of battery storage based on its electric vehicles’ batteries, with the goal to reach up to 400MW by 2030.
On a smaller scale, Voi recently donated batteries from its initial scooter model as power banks for war journalists in Ukraine. Despite the lower potential impact of the solution, it highlights the large range of applications still unexplored for a battery's second life.
When it comes to recycling, most European countries have set up their own industry. Paprec or Corepile in France, Recover or LBRS (who recently partnered with Voi) in the UK, GRS Batterien in Germany… Options exist. But Julian Ahlers, Sustainability Manager at TIER, warns that “the recycling capacity for Lithium-Ion batteries in most European countries is already not matching the need”. With the growing adoption of electric vehicles, additional capacities are needed, but we are still in the early development stages. TIER nonetheless scaled its commitment to recycling its batteries with a recent partnership with Remondis across 16 countries, representing a total of 160,000 units.
Given the 3 to 4-year theoretical lifespan of a Lithium-Ion battery for shared mobility use, it is also worth noting that few batteries still need to be recycled, as most vehicles have not been running for so long. Paul-Adrien Cormerais mentions that “Apart from the Segway ES4 we initially launched, which batteries were noticeably failure-prone, we are currently not shipping any batteries to recycling. All are being repaired or used for R&D purposes by our partner Gouach”. It highlights that battery quality has greatly improved over the years, but also that the multiple iterations in vehicle design can lead to significant waste, just because they won’t be compatible with the following model(s).
Aside from volume, there have been a lot of developments in the quality of recycling. Traditional methods such as pyrometallurgy and hydrometallurgy, are expensive and time-consuming and don’t recapture all of the valuable materials inside. Battery recycling companies are in a golden age to scale up their technologies to make Lithium-Ion battery recycling more efficient, clean and profitable.
A few years after the EV boom, its time for the battery recycling boom, which will be answered better with:
- New recycling processes, such as disassembling batteries down to the cell's components (instead of shredding),
- Focusing on retrieving the rare metals
- Powering the recycling process with the power stored in the old batteries.
The low-down
There are many ways operators can improve their environmental impact: from developing new battery technologies to adopting AI-based battery management systems and exploring second-life opportunities. The rapid growth of the electric car industry will certainly boost the development of these solutions with higher investments. Shared mobility operators will, of course, provide their full support, as they crave to improve their environmental impact, both to answer the environmental requirements from local authorities in tenders, and to protect what they believe in: fighting climate change. There is no time to waste!
Written by Alexandre Gauquelin (Shared Micromobility), in collaboration with Julien Chamussy.
Never miss a street.
Want to be the first to hear about new launches, quiet exits, public policy developments, tenders, fundraising and more?
Stay up to date with all the latest news and insights delivered straight to your inbox. Subscribe to Fluctuo’s weekly newsletter